Ok well first, the ribs on the front plate add virtually nothing but weight because the plate is fastened directly to the bearings with no overhang, it's also short and strong so very little vibrations come from that area.
Regards the plates on the sides then these would help, however, I have a better suggestion. If you look at the pic and at the other machines I've built I always put a cover over the Z-axis. This isn't just to protect from debris it's also structural as it does the same job those plates. You don't need a 10mm plate, I use 3mm for the covers and it's more than strong enough.
The spindle mounting area is limited to the lower area (see the pic, it's the silver area, the black is drawbar cylinders.) However, they are steel and would easily handle another clamp.
Regards putting the spacer plates on the front plate to save weight then I wouldn't do that either because of your shifting weight to the wrong area.
To be honest I wouldn't use spacer plates as it lowers precision and makes it complicated.
Regards Motor brake then I can't answer that because I don't know those motors, but servos are not like steppers where they have a shaft sticking out the back, mostly because this is often used for the encoder.
How the motor handles the weight will depend on usage, but if you plan on doing 3D type work with lots of short moves with high acceleration then I think they 180W motors will struggle with the inertia and you'll get some following errors. Because again servos are unlike steppers where if they lose the position you visually see the lost steps, instead the encoders along with the drives close the loop and catch back up so will always return to exact same place when stopped provided they don't go outside of parameters set in the drives.
However, what you get is a following error which if it stays within following error parameters can trick people into thinking they don't have a problem because if they do a type of work which is mostly 2D the Z-axis isn't whizzing up & down so it gets missed.
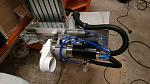
Bookmarks