Work has been getting in the way of progressing my machine, but where I left off the laser system is working well enough to perform the operation (particularly with the raspberry pi version) however the process of position a jig and routing the steel frame into plane with a trim router was highly error prone.
1. It was difficult to level the jig since I didn't use concentric adjustment and clamping bolts,
2. The process requires that the laser doesn't move, the trim router height gauge doesn't move and the cutting tool doesn't break or chip throughout otherwise it has to be started over. Also the jig has to remain a planar plate and not wear, since I used tooling plate the surface got quite a lot of wear from the trim router.
This is what stopped me attempting it across the whole machine frame.
So I've had a bit of a rethink and come up with a different process that is hopefully a bit more forgiving and controlled. Rather than attempt to level the frame by grinding it the new processes will attempt to attach rail bearing sub plates to the frame such that these sub-plates are planar.
I'm thinking of using 10mm aluminium for the sub-plates. The plates would run the full length of the X axis on top of each steel beam and eventually the rails will be bolted to these plates. The plates will themselves be bolted to the steel frame in an adjustable manor such that they can be brought into plane using the laser, then they will be permanently fixed in place with a potting compound taking up the gap between plate and frame.
A few people have tried this using set screws to level the plates which seems quite fiddly unless you go the trouble of making concentric adjustment/locking bolts.
What I'm proposing is to take each plate and drill two sets of holes along the centre line. The first set will be counterbored and used to bolt the plate down to the steel frame, the second set will be used to inject the potting compound. To allow the plates to float above the frame but also be held accurately in height by the bolts I'm thinking a compressible gasket could be run down each side of the plate. As the bolts are tightened the gasket would compress pushing the plate up hard against the bolt, this is simpler than grub screws and locking bolts.
To prevent the two plates (one for each X rail) tilting they would be coupled together with lengths of angle during the process.
The laser would be setup and both plates adjusted into plane using the bolts, once everything is level potting compound would be injected through the remaining holes. The compressed gasket will now act to contain the potting compound.
I think this has a number of advantages,
1. The entire leveling process can be completed before making a permanent adjustment to the machine,
2. I would be directly leveling the final machine surface (the sub-plate) rather than some tool that is then used to machine the frame.
I have sketched this up, would welcome thoughts on it.
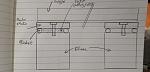
Bookmarks